Stock Control Software: Why Your Trades Business Needs This
March 16, 2023 | Read: 10 minutes
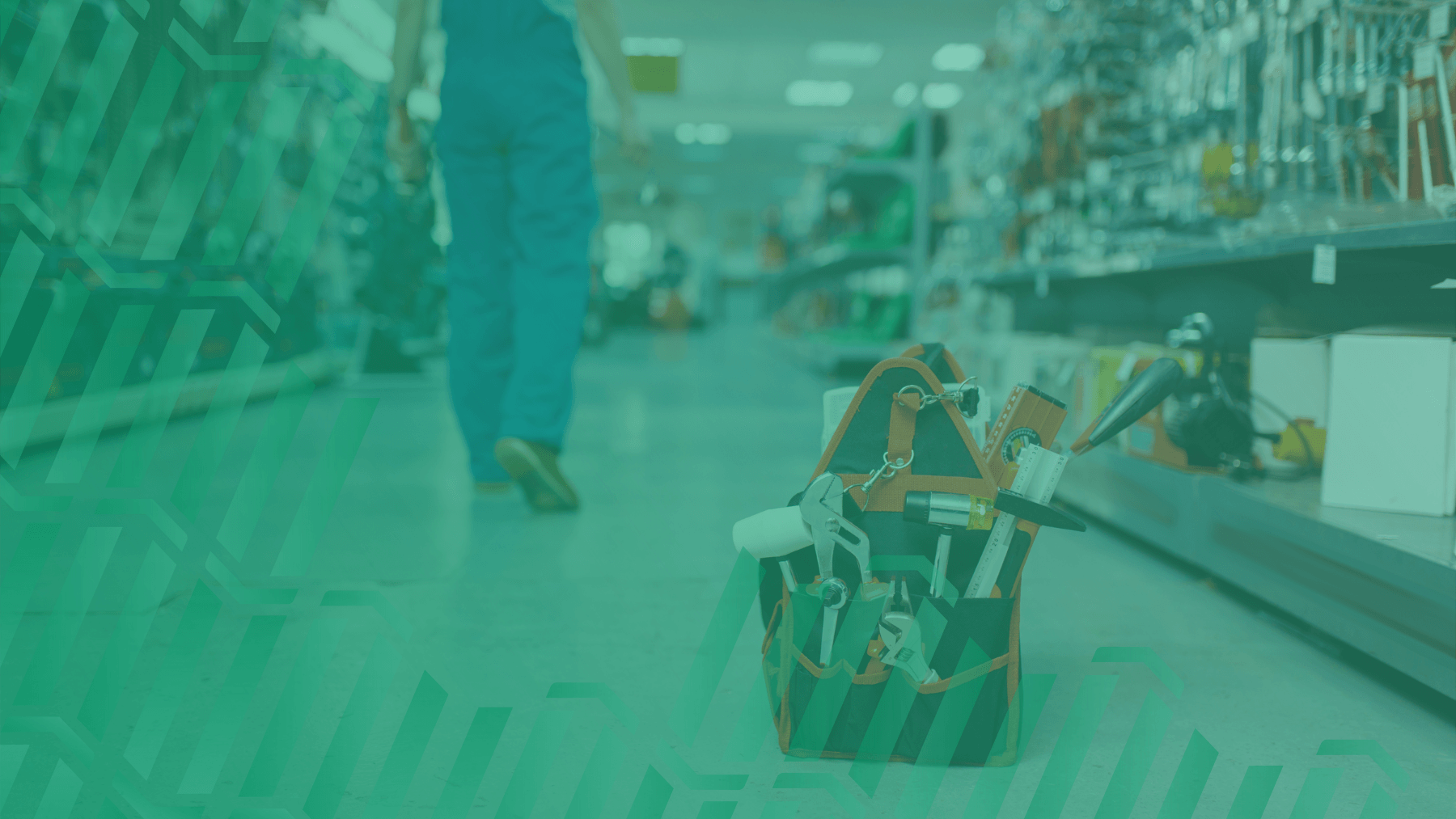
Think about your current inventory management system: is it a smooth running process, or a logistical mess?
A stock control software, with automated ordering, can drastically reshape your operations.
The right parts management tools enable your team to take full control over stock. Here are seven can’t-miss features your next inventory software should include.
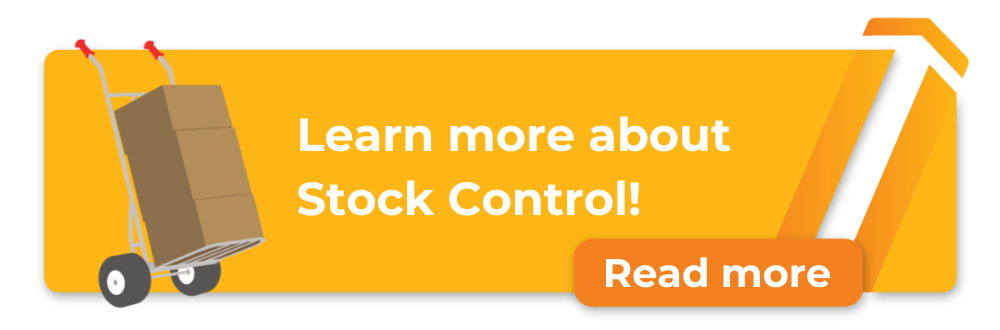
1. Access to Real-Time Stock Levels
Knowing how much inventory you have, and where they are is difficult without a stock control software. Each minute of the working day is valuable. Searching for parts, mistakenly stockpiling inventory, and losing parts will eat away at both productivity and company revenue.
Breaking this mold is daunting, but controlling all aspects of inventory effectively is necessary for a growing field service business.
Real-time knowledge of all aspects of your company stock, managed by an stock management software, will optimize your daily operations. Improving efficiency and supporting the synergy of your team is where stock control software shines.
Real-time availability tracking marks parts reserved for jobs, which are being returned, and what your next order looks like. With real-time inventory knowledge at your fingertips, your team can stay prepared for any situation.
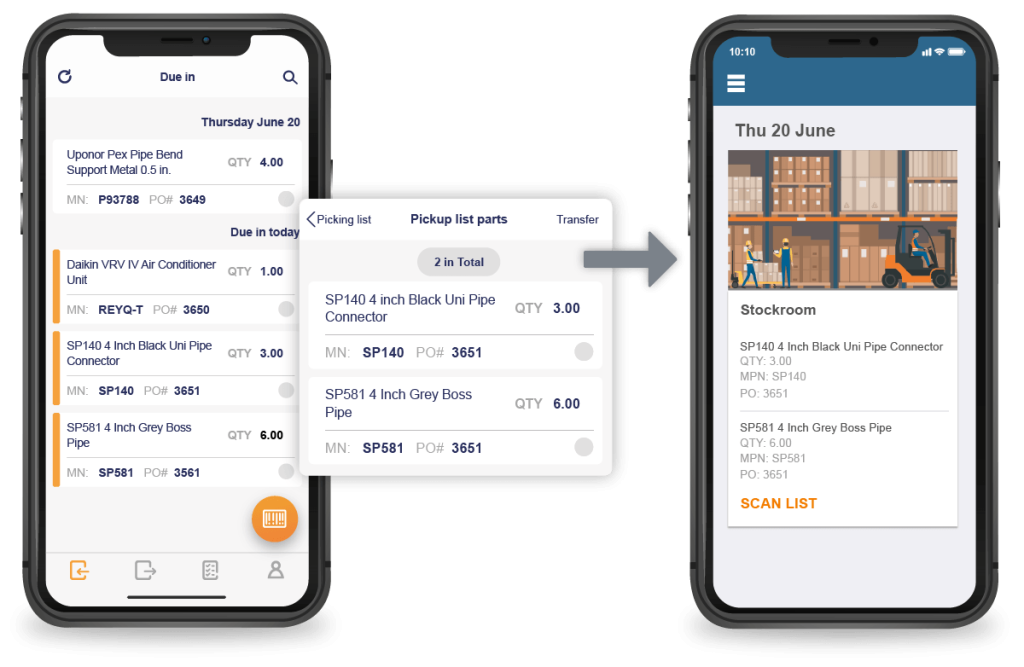
When your technicians are on site and need a specific part, they won’t need to call the back office or check the stockroom. Up-to-date stock data will be available from their smartphone. They’ll know if and where they can find the part.
For your business, this means less admin time and consistently using existing stock before purchasing more. For your customers, it means faster job completion and ultimately, greater satisfaction.
Of course, your stock management database also comes in handy when the required parts are not currently available. Knowing for certain that the part is out of stock gives you the confidence to put in an order.
This takes us to the next essential feature of stock control software – automatic reordering.
2. Automatic Reordering to Stay Prepared
Inherently, many aspects of the ordering process are out of your hands. Your team can’t control how long it’ll take for a part to arrive. But you can cut time when placing a typical order.
If your technicians don’t have the right parts, at the right time, your customers will book future jobs with better-prepared competitors. Put yourself in their shoes; wouldn’t you do the same?
The more streamlined your ordering process, the better. Stock control software should cut down on ordering time while helping your stockroom manager and technicians. An automatic reordering system is an option that ensures you’ll always have the standard parts your team utilizes available.
For example, you could set your software to always keep a stock of ten blue widgets and 20 red widgets. As soon as the stock level drops below those numbers, the system will automatically order more in your pre-defined quantity. With an automated tool like this, you can guarantee that essential, everyday items will always be in stock for your team.
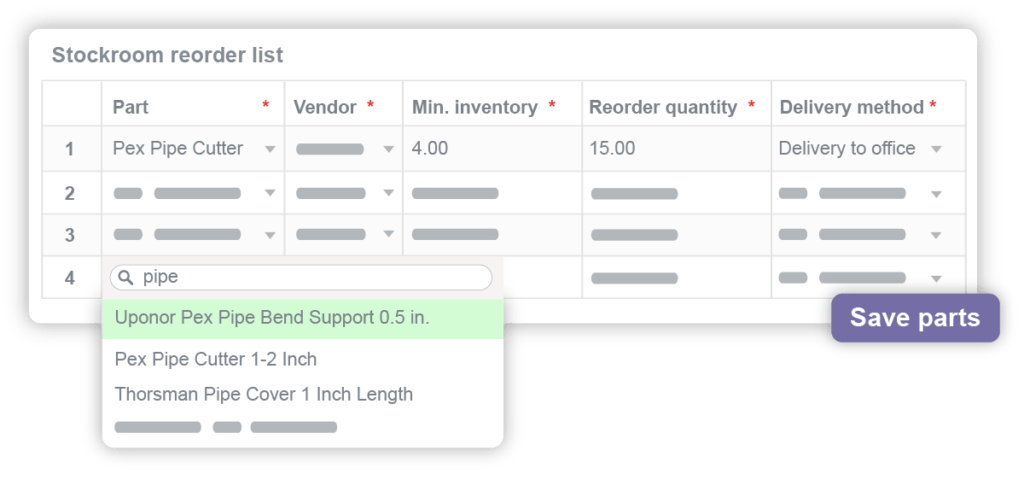
Automatic reordering can account for jobs where your technicians are expected to have the right parts upon arrival. But these jobs aren’t the only situation your company will face.
This leads us to our next stockroom database system feature: purchase orders.
3. Purchase Orders in the Field
A call-out, or diagnosis job offers another avenue to utilize the full capabilities of an inventory management system. In these situations, there’s a reasonable chance technicians won’t have the correct part in their truck or the stockroom. Getting parts to customers as soon as possible is a must. Technicians need to be able to place orders from the field with minimal effort.
For some businesses, technicians need to call the office, relay the request, and then wait for the order to be processed. This process relies on several people to get one order placed. This adds avoidable time to the workflow and delays the job’s completion, resulting in a less happy customer.
Here’s an optimized stock workflow: A technician needs a part, so they immediately place an order on their mobile phone app. The best apps will incorporate the costs and PO record logged against the job. They then have the best chance of the part arriving sooner and completing the job promptly.
The best solution automatically oversees stock and helps teams refine the ordering process. Your company can always be looking forward, rather than catching up.
Once parts arrive, your stockroom manager must have a smooth workflow and tools to get everything inputted correctly.
4. Mobile Bar Code Scanner for Easy Check-Ins
A long and tedious check-in system leads to mistakes. A barcode scanner, acting as a further extension of your field service inventory management solution, can slash errors while saving time. If you’re imagining a handheld scanner like those at a grocery store, you’re thinking too big. A bar code scanner mobile app is an efficient and economical solution that can heavily improve your parts check-in process!
When new parts arrive, instead of manually recording data like name and product number into a spreadsheet (or even worse, a paper-based log), this lightweight solution allows your team to quickly scan the part’s bar code, select the quantity, and add it to your inventory.
Checking in a new part should be easy too. After the first scan, you simply assign the bar code to the new part. The system will now recognize it going forward.
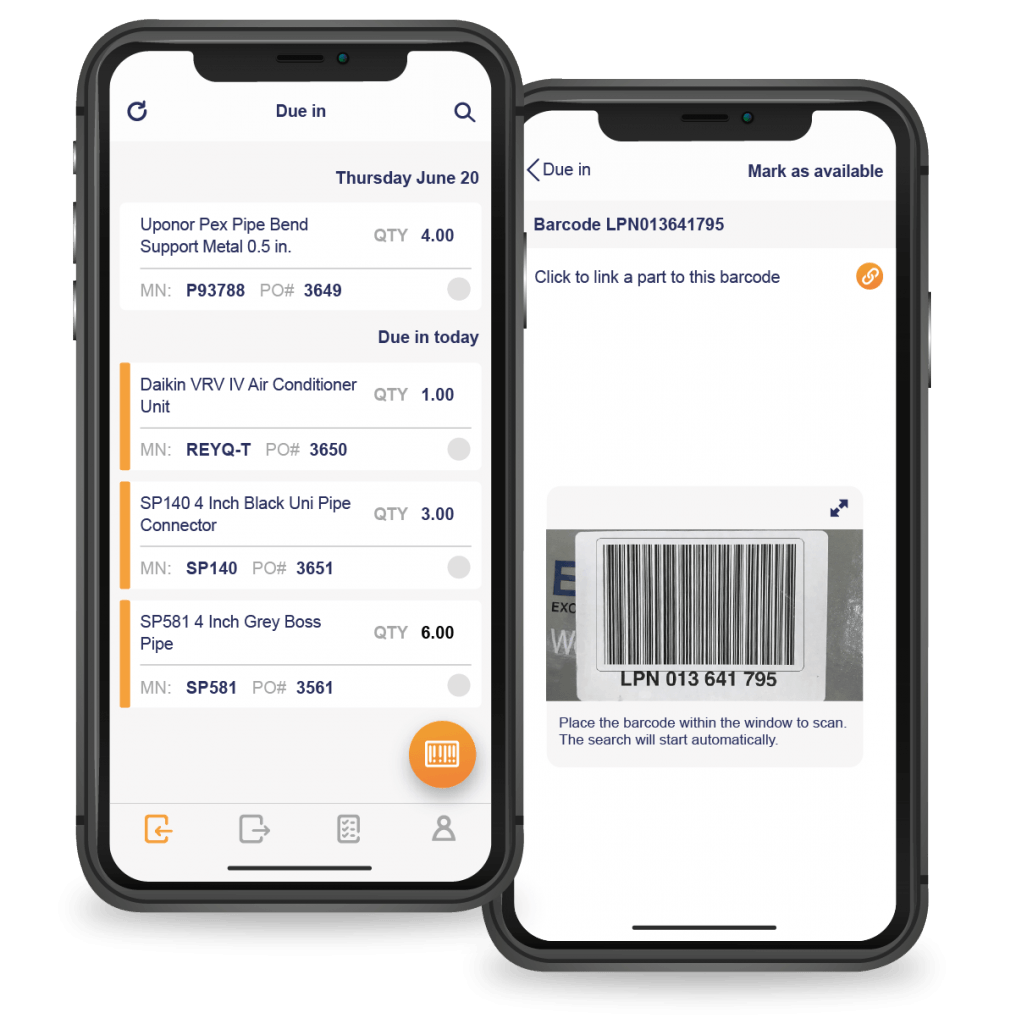
An intuitive barcode scanner built into your multi-location inventory management software can help your warehouse manager check in new deliveries.
Plus, all newly checked-in parts will automatically sync to your database. This means your up-to-date stock levels will be accessible to your office staff and technicians right away.
But checking in stock is only part of a stockroom manager’s responsibilities. Once everything has arrived it then needs to be organized!
5. Efficient Picking Lists
Transitioning new parts from your warehouse to your technicians’ vans can take up a lot of admin time. Managing this movement via spreadsheets can be a time-consuming and chaotic process. It doesn’t have to be this way. A stock management software can accurately facilitate the movement of inventory from your stockroom to your company fleet.
Think about it, shortening the transfer time means your team can get on the road quicker. This gives them the capacity to complete more jobs. When parts need to be moved from the stockroom to your trucks, picking lists can keep your team on schedule.
Picking lists are noteworthy because of the accountability and organization they bring to your stock management. By having a location assigned to each list, like “Warehouse”, or “Tony’s truck”, your warehouse manager can oversee the correct movement of parts to various locations.
Building a picking list should be easy too!
For example, if the warehouse manager can see all the parts needed by a technician, by date, they can logically build a list for each technician. All that’s left to do is to physically prepare the necessary parts for the team. When the technicians arrive at the warehouse, they’ll need to confirm that they have collected the parts.
This inventory database management system logs the transaction and seamlessly transfers the parts from the warehouse to the technician’s truck.
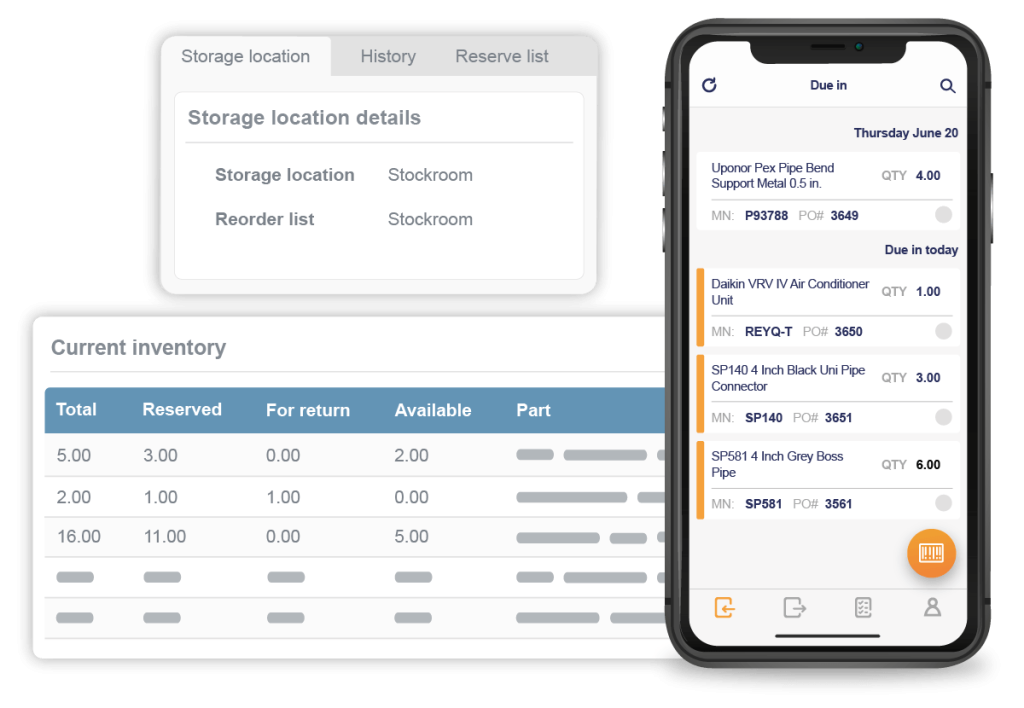
Stock database software supports the ability to build customized picking lists. With this, you can streamline a vital aspect of your day-to-day stockroom workflow and get parts out to technicians quickly.
Once that’s done, it’s essential to give your crew control over the stock that they are storing in their trucks.
6. Track What’s in Your Trucks
Your technicians play a vital role in stock management, and they deserve to be ingrained in your inventory operations. Involving them with stock, with all important information accessible on their smartphones, will further cut down time and increase productivity.
Most stockroom software fail to recognize the importance of your technicians and their vans: this is a large mistake. Knowing what parts are in your storeroom is a necessity. But knowing exactly what parts are in your technicians’ vans is important too. After all, they function as mobile stockrooms.
Company stock spread across multiple locations is common in field service, and your stock management solution needs to reflect this.
A stock control software that supports multi-location functionality should empower technicians to track exactly what is in their truck. It should also give them the power to make transfers while out on the road.
Forgoing the picking list process, if Tony the technician needs a part, and knows Bill, another technician has the part in his truck, they can meet up. They can exchange the part, and record the transfer within the company database using their smartphones. Tony doesn’t have to drive all the way back to the warehouse. He can install the part and complete the job quickly.
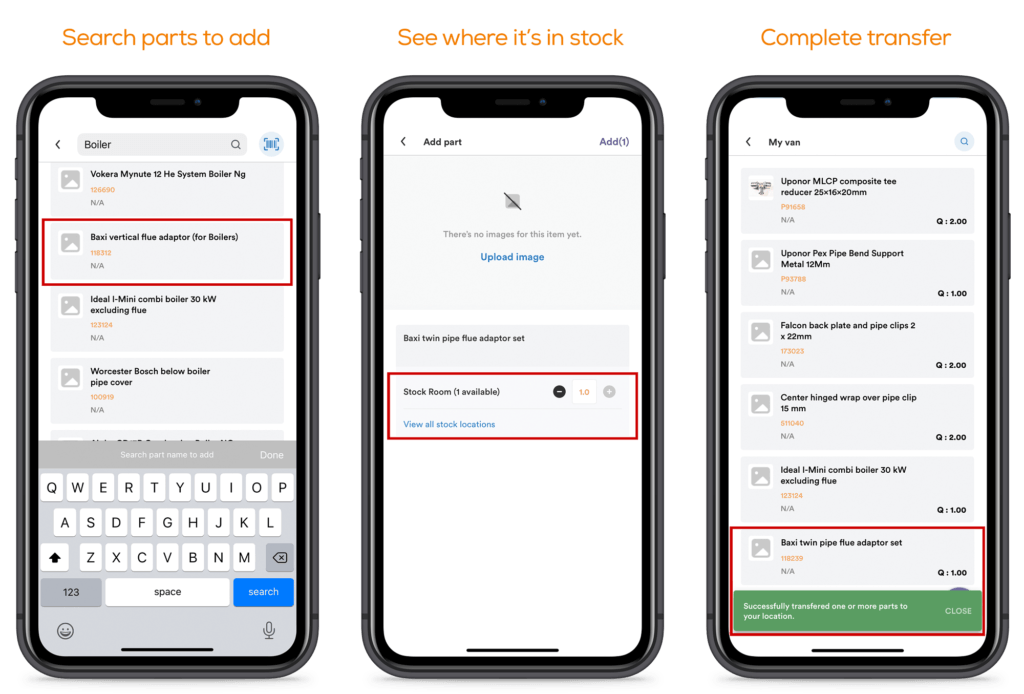
Additionally, the ability to search from their smartphone to see what’s in their truck can save time spent rummaging around looking for certain items. No matter what the day brings, your technicians can be supported and feel in control of their own stock.
Sometimes parts go unused and may not be required for other jobs. This is where our final feature comes in – streamline stock returns.
7. Streamlined Returns Workflow
How often are you returning parts? Never, or rarely returning parts to vendors can be the result of two situations. The first means that your stock management solution is currently working well enough to limit overstock.
The second indicates that your current inventory database isn’t accounting for lost parts and backstock. Piles of unused parts at the back of your warehouse is a costly use of both your company’s budget.
Equally, when parts are left in trucks too long, they’re prone to becoming lost or broken. Across your company fleet, if left unmanaged, this practice will slowly, yet steadily, chip away at your company profits.
With the right software, you can mark items for return, track their progress and current status, and communicate with vendors. By ensuring a transparent returns process, you stand a better chance of completing the return and recouping your investment quickly.
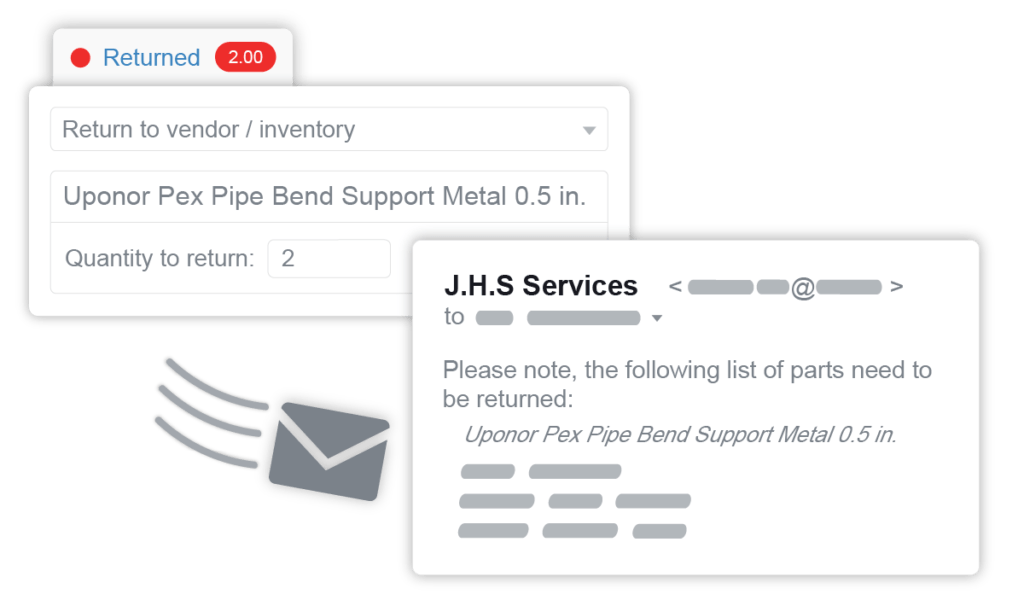
Being able to easily return unused parts to vendors should be a regular aspect of your stock management system. Inventory returns software will support your company’s growing cash flow and help your team keep track of each and every part.
Transform Your Parts Operations With Stock Control Software!
A dependable stock control software will function as an essential assistant to your warehouse manager and technicians. As your business grows, you can stave off the common stock pitfalls and problems that field service businesses face. Instead, your warehouse and parts management systems will remain organized and uncomplicated.
As covered above, seven revolutionary features to include are…
- Real-Time Inventory Levels
- Automatic Reordering
- In-The-Field Purchase Orders
- Mobile Bar Code Scanning
- Picking Lists
- Truck Inventory
- Returns Management
If these solutions sound like the perfect fit for your trades business, Commusoft’s field service inventory management software is for you! Our all-in-one job management software efficiently simplifies day-to-day tasks, increases team productivity, and scales your profitability.
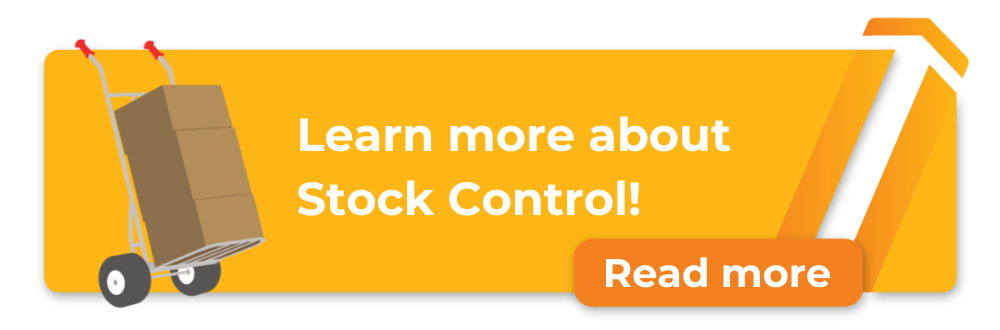
Emma Bozenda
When I'm not writing about the best digital solutions for trades businesses, I'm either playing with my three dogs, or baking sweet treats!